PRODUCT ENGINEERING service
45+ years of engineering high-performance,
reliable solutions across complex systems
powered by Psycho-Aesthetics®.
VGX‑Inovio – Engineering Scalable DNA Vaccine Delivery
A patient-ready electroporation device that delivers DNA-based vaccines with accuracy and safety.
Meritech CleanTech® EVO Smart Handwashing Stations
Smart, automated hygiene engineered for maximum safety and sustainability
Synaptic Cryoablation System
Revolutionizing Cardiac Care with Accessible Innovation.
Engineering reliable, smart design
RKS is a product engineering firm focused on the process of designing, developing, prototyping, and testing innovative products and services. We are here to aid our clients with any product engineering need, from new to existing products.
As a leading product design and product engineering development firm, we use our human-centered methodology to solve complex engineering challenges. We help our clients with all aspects of a product’s life cycle, from the product idea to the final product. Our in-house teams of specialists, researchers, industrial designers, and engineers leverage their multi-industry knowledge to spark creative, innovative solutions. We leverage our full-service CNC and prototyping lab to handle any project. Our expertise and product engineering services include CAD development, BOM creation, CTF drawing, prototyping, 3D printing technology, and testing. We leverage our mechanical problem-solving, materials sourcing, and manufacturing support to assist our clients every step of the way.
3000+
Interviews
60+
Projects
56+
Global Cities
Psycho-Aesthetics® & Product Engineering
The engineering design process is a common series of steps that engineers use in the product engineering of any successful product.
Our innovation consulting process begins with our Psycho-Aesthetics® Methodology. Pyscho-Aesthetics is a process that entails defining a precise definition of vision, mission, objectives, and critical results. Building this strategy is a collaborative consulting process between our client stakeholders, business partners, and team. Our methodology, Psycho-Aesthetics®, is a sophisticated design-thinking tool. It assists our team in solving business problems by using an objective, pragmatic, and insightful approach to innovation consulting. This shared approach helps us to reach our objectives.
Engineering Research
Research Capabilities
Engineering Testing
Our engineers perform engineering verification tests (EVT) on first prototypes to determine whether it meets specifications and design goals. Our engineers develop test programs and QC documentation, perform testing, and analyze defects identified in testing. Our mechanical engineers have a deep understanding of mechanical properties to optimize engineering verification tests.
Compliance and Regulatory
To manufacture a product, product development, and engineering teams must adhere to regulations. Our engineers work hard to meet compliance requirements set by governments, industry associations, and our clients. Some examples include FDA certification, CLIA Certification, ISO and 13485 Compliance, and European Medical Devices Regulation (MDR). We adhere to standards that our clients and their regulatory partners define as they navigate these issues.
Materials Science
Successful design to manufacturing requires an understanding of materials science and engineering. Materials engineering is the task of applying materials science knowledge to the creation of products and manufacturing designs. We leverage our materials science expertise to ensure products meet performance, reliability, and cost requirements.
Patent Protection
We offer patent services for every engineering and development project. Our data protection and procedures actively ensure the protection of the rights of our clients and their company. Often our engineering design produces valuable and game-changing innovations. These innovations can change a company dramatically, and we take our responsibility of protecting these sources of growth seriously.
CAD
Our designers and engineers use computer-aided design (CAD) to create designs in 2D and 3D. Our established 3D printing processes assist our team in visualizing the construction of a product. This enables efficient design, development, and modification for post-processing.
We utilize CAD to aid us in solving engineering challenges. Solving complex problems requires a combination of organization, analysis, problem-solving principles, and a graphical representation of the problem. CAD allows us to visualize attributes like height, width, material, and colors before we put a design into development.
Product Engineering Methods
Our in-house prototyping lab sets us apart from competitors. Our innovative 3D printing methods take us to the next level. We utilize a combination of engineering methods and manufacturing processes that I’ve us a unique advantage in product engineering. Our systems engineering methods incorporate traditional systems integration and innovative technologies like hybrid cloud, AI/ML, and IoT. Through decades of experience, we have established best practices for every product engineering project and method.
Design Engineering
Development Capabilities
Rapid Prototyping & 3D Printing
Rapid prototyping allows us to create and test products to optimize specific attributes. We utilize computer-aided design (CAD) to rapidly create digital parts, pieces, or assemblies.
We implement our 3D printing or our CNC capabilities to create physical products. Our rapid development prototypes benefit our clients as they allow us to create quick production processes with efficient turnaround.
We integrate selective laser sintering (SLS) and fused deposition modeling (FDM) into rapid prototyping, ensuring an efficient time to market.
Vendors and Material Sourcing
Our suppliers can often be a great source of innovative ideas for future products. Through close relationships, our suppliers have the freedom to support engineering and innovation efforts. This can result in a competitive advantage for both our clients and the supplier.
Our relationships with different suppliers usually serve two purposes. First, they allow us to compare prices. Second, they provide us with a backup plan in case one of our suppliers is unable to complete the job.
Manufacturing Engineering Support
Our clients often seek us out for product engineering help. We aid them with our deep experience and efficiency in moving a product from engineering to production. Our manufacturing support connects our clients and suppliers with our manufacturer partners to support all or specific parts of the process.
At the outset, we help our clients find the right manufacturers for their products. We assist in sourcing sub-assembly and parts configuration used in a manufacturer’s products, reducing labor and storage costs. We offer “post-production” services such as packaging design and sourcing. Removing the burden of work from the manufacturer and client.
Product Engineering Across Markets
We have decades of experience in new product development. We have gained recognition for applying our product engineering competencies to various industries and markets. We have designed and engineered many different products for clients all over the world. Though there are common challenges for each industry, each project brings its own unique challenges and opportunities. We approach each challenge with the same experience and skills that enabled us to create lasting value for our clients.
Engineering Expertise
Industry Expertise
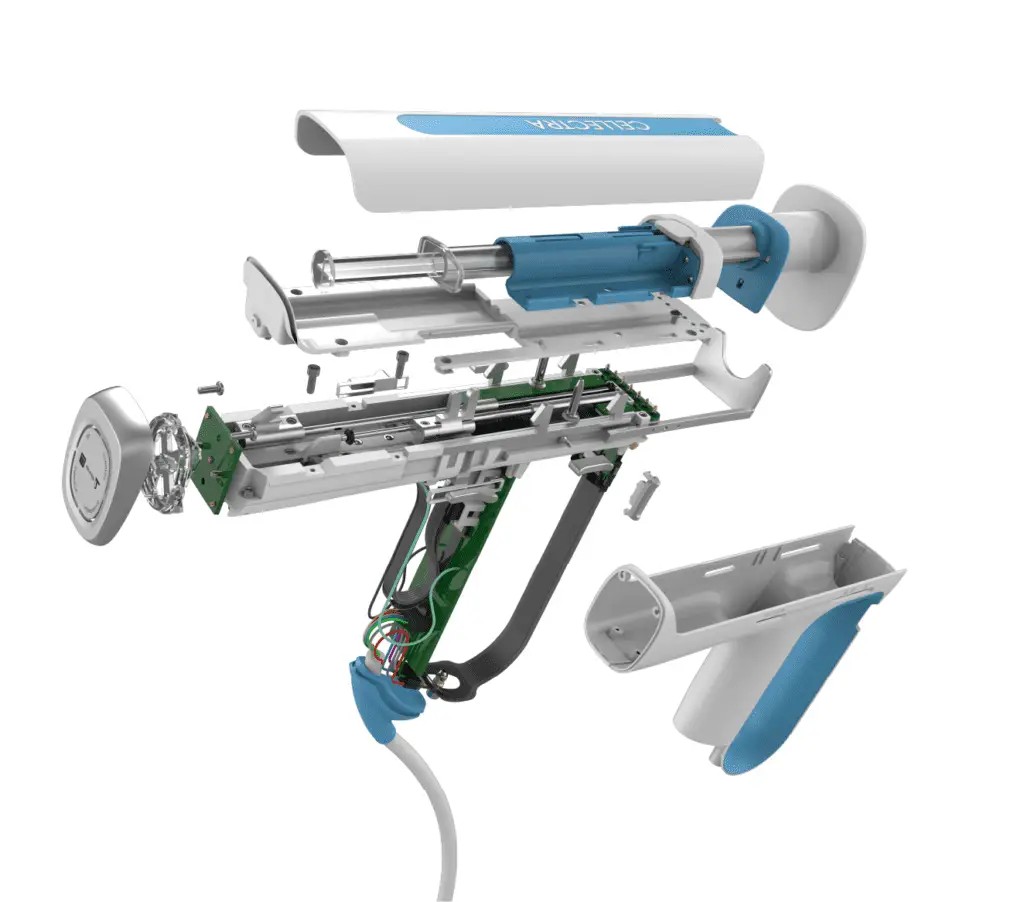
Medical Devices
We specialize in Class I–III medical devices, combining usability engineering, risk mitigation, and DFM to deliver regulatory-ready innovations. From ergonomic surgical tools to connected drug delivery systems, we ensure safety, accuracy, and compliance at every step.
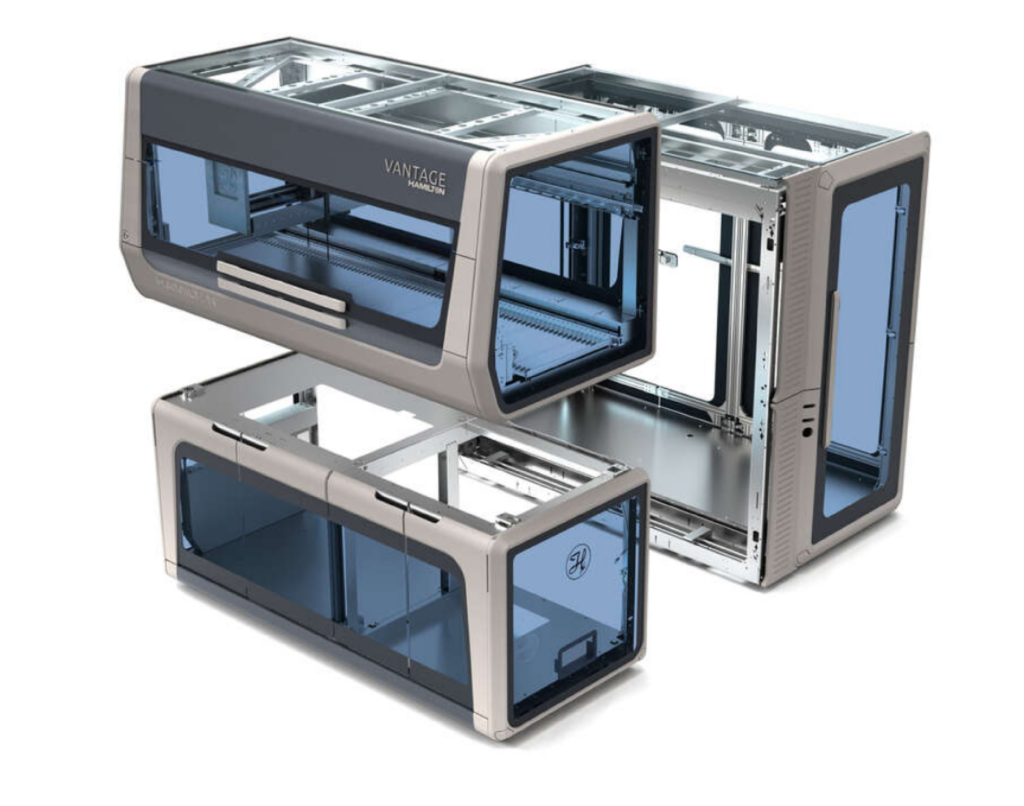
Life Science Instruments
Our team develops high-performance platforms for genomics, diagnostics, and molecular biology. We bring together system architecture, precision mechanics, and user insight to create instruments that enhance workflows and scientific accuracy.
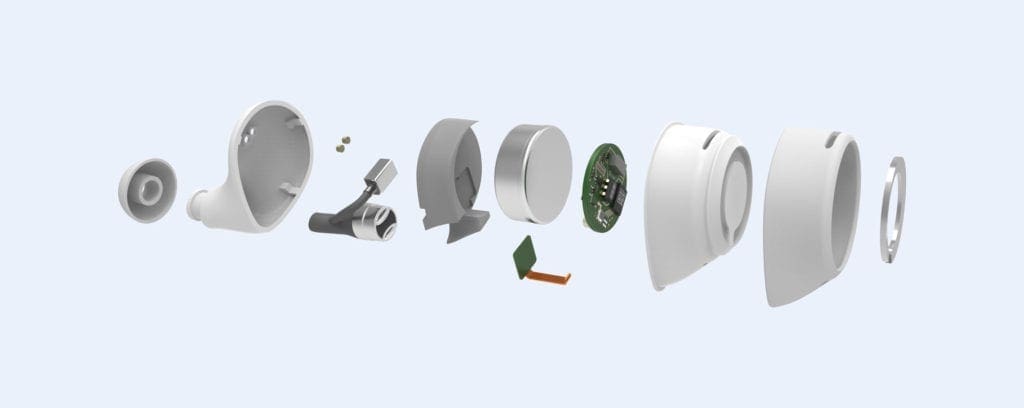
Consumer Electronics
From wearables to smart home tech, we create consumer products that are as functional as they are beautiful. Our engineers and designers work in lockstep to optimize for user interaction, manufacturability, and brand differentiation.
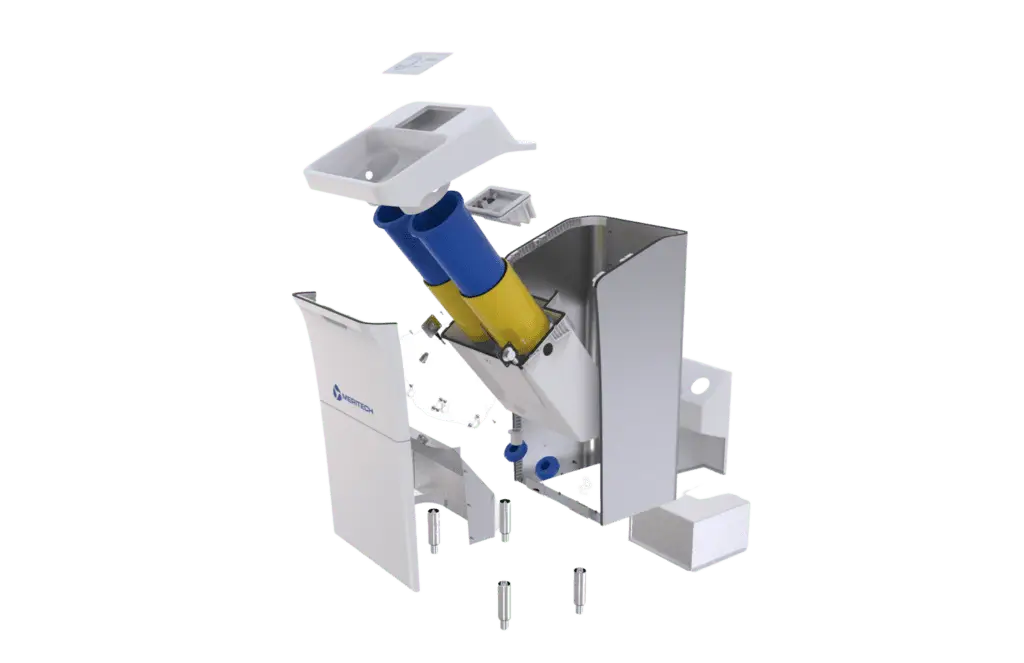
Commercial Products
We specialize in Class I–III medical devices, combining usability engineering, risk mitigation, and DFM to deliver regulatory-ready innovations. From ergonomic surgical tools to connected drug delivery systems, we ensure safety, accuracy, and compliance at every step.
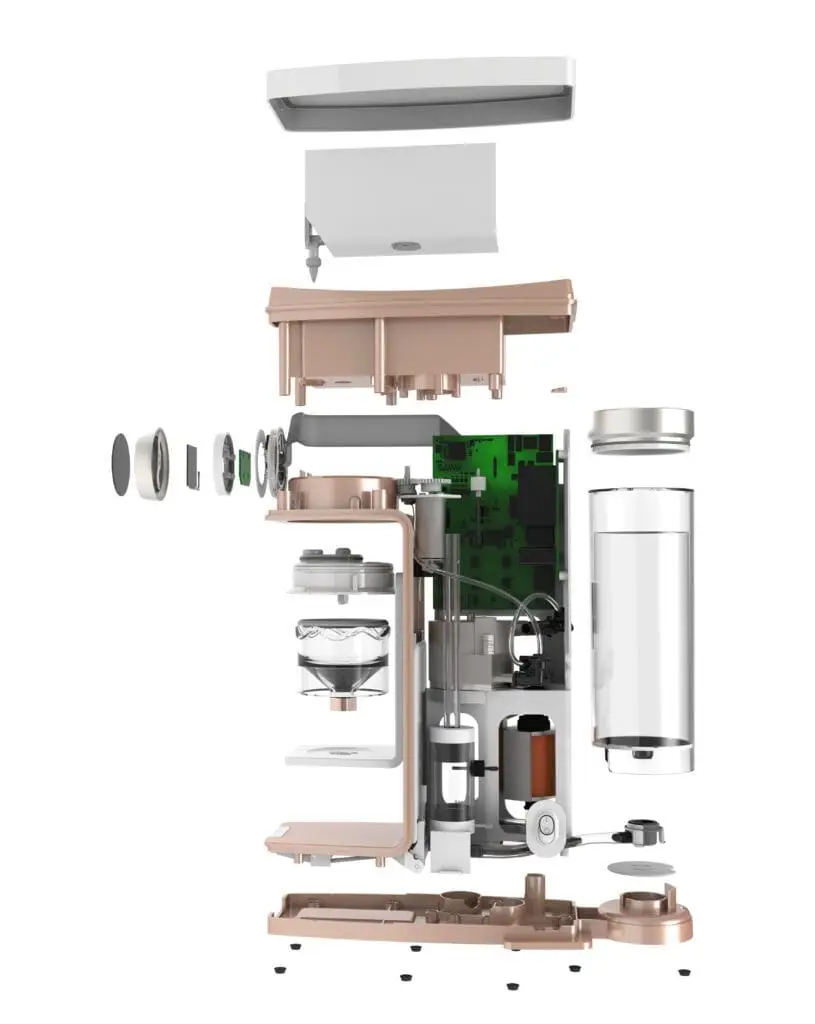
Home Appliances
We combine intuitive UI/UX, CMF strategy, and mechanical design to bring household appliances to life. Whether it’s a countertop device or connected smart appliance, we balance design intent with engineering feasibility for market-ready performance.
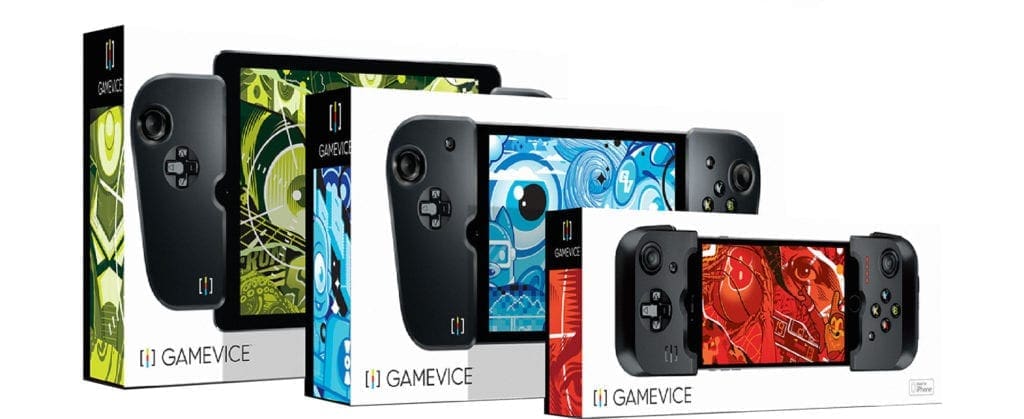
Consumer Packaged Goods
From ergonomic packaging to reusable systems, we engineer CPG solutions that maximize usability, manufacturability, and sustainability. We prototype, test, and optimize for form, function, and brand experience.
ready to partner with us?
What does product engineering include?
Product Engineering is a highly collaborative process that includes cross-functional collaboration between designers, researchers, and engineers. The product engineering process typically begins with a concept or idea, which is then refined and tested through various stages until it is ready for mass production and distribution. The first step in the product design engineering process is design. At RKS this involves using Psycho-Aesthetics® to identify the needs and desires of the target market, as well as the product’s unique selling points and differentiators. This phase also involves identifying potential materials and manufacturing processes that will be used to create the product. Once the concept has been defined, the next step is to create a detailed design of the product. This typically involves using computer-aided design (CAD) software to create a 3D model of the product. The design process also involves defining the product’s dimensions, functionality, and other key characteristics. Once the product’s design has been finalized, the next step is to create prototypes for testing. These prototypes are used to evaluate the product’s performance and identify any potential problems or issues that need to be addressed. This phase may also involve testing the product’s design under a range of different conditions, such as different temperature and humidity levels, to ensure that it is able to withstand the demands of real-world use. Once the product has been prototyped and tested, the next step is to prepare it for mass production. This typically involves creating detailed manufacturing plans and processes, as well as identifying and procuring the materials and components that will be used to create the product.
Throughout the product design engineering process, product designers must work closely with other teams and departments, such as research and development, marketing, and sales, to ensure that the product meets the needs and expectations of the target market. This may involve conducting market research and gathering feedback from potential customers to help inform the product’s design and development. In addition to the activities described above, product design engineering may also involve identifying and implementing new technologies and manufacturing processes that can improve the product’s performance or reduce its cost. This may involve working with suppliers, vendors, and other partners to identify and develop new materials and technologies that can be used in the product’s design and manufacturing. Product design engineering is a complex and multi-faceted field that involves a range of activities and disciplines. It requires a deep understanding of market needs and trends, as well as technical expertise in areas such as CAD design and manufacturing processes. By combining these skills and working closely with other teams and departments, product design engineers are able to create innovative and successful products that meet the needs and expectations of consumers.
What is product design in mechanical engineering?
Product design in mechanical engineering is the process of creating and developing ideas for mechanical products and systems. This involves a combination of engineering principles, design techniques, and creative thinking to come up with innovative solutions that are both functional and aesthetically pleasing.
Mechanical engineers are responsible for designing and developing a wide range of products, from small components like screws and gears to complex systems like engines and machines. In order to do this effectively, they must have a deep understanding of the principles of mechanics, materials science, and manufacturing processes. The product design process in mechanical engineering typically begins with identifying a need or problem that needs to be solved. This could be something as simple as a more efficient way to open a jar, or as complex as designing a new type of airplane engine. Once a need has been identified, the mechanical engineer will conduct research and develop a number of potential solutions. This may involve testing different materials, creating prototypes, and conducting simulations to evaluate the performance and reliability of different designs. Once a solution has been selected, the mechanical engineer will create detailed technical drawings and specifications that can be used to manufacture the product. This may involve working with other engineers, designers, and manufacturing experts to ensure that the product can be produced efficiently and cost-effectively. In addition to technical considerations, product design in mechanical engineering also involves considering the aesthetic and ergonomic aspects of the product. Mechanical engineers must be able to create designs that are visually appealing, easy to use, and comfortable to hold or operate.
Product design in mechanical engineering is a complex and challenging process that requires a deep understanding of engineering principles, design techniques, and manufacturing processes. It is a critical part of the development of many of the products that we use in our daily lives, and it requires a combination of technical expertise, creativity, and problem-solving skills.
What is the difference between product design and product engineering?
Product design is the process of creating a new product or improving upon an existing one. It involves researching, conceptualizing, and developing ideas for a product that meets the needs and wants of the target audience. This process typically involves brainstorming sessions, sketching out ideas, creating prototypes, and conducting user testing to ensure the product is functional and appealing to customers. Product design engineering, on the other hand, focuses on the technical aspect of product design. It involves the application of engineering principles and techniques to the design process. This includes analyzing the product’s functionality and performance, as well as determining the materials and manufacturing methods needed to produce the product. Product design engineers are responsible for ensuring that the product can be manufactured efficiently and meets all safety and regulatory requirements. One key difference between product design and product design engineering is the focus of each discipline. Product design is more focused on the user experience and aesthetic appeal of the product, while product design engineering focuses on the technical aspects of the design and how it can be efficiently manufactured. Another difference is the skill sets required for each discipline. Product designers typically have a background in design or a related field, such as industrial design or graphic design. They may have expertise in areas such as user research, sketching, prototyping, and user testing. Product design engineers, on the other hand, typically have a background in engineering, such as mechanical or electrical engineering. They may have expertise in areas such as materials science, manufacturing processes, and engineering analysis.
In many cases, product design and product design engineering overlap and work together to create a successful product. For example, a product designer may create a concept for a new phone, and a product design engineer may work on the technical aspects of the design, such as determining the materials and manufacturing processes needed to produce the phone.
The main difference between product design and product design engineering is their focus and skill sets. Product design focuses on the user experience and aesthetic appeal of the product, while product design engineering focuses on the technical aspects of the design and its manufacturing feasibility. Both disciplines play a crucial role in the product development process and often work together to create successful products.
How do you become a design engineer?
Becoming a design engineer requires a combination of education, experience, and skill. The first step to becoming a design engineer is usually to obtain a bachelor’s degree in a field such as mechanical engineering, electrical engineering, or industrial design. This degree will provide you with a solid foundation in engineering principles and design methods, as well as a general understanding of the various fields of engineering.
After earning your bachelor’s degree, it is important to gain experience in the field through internships or entry-level positions. This will give you the opportunity to apply your knowledge and skills in a real-world setting, while also gaining valuable hands-on experience.
In addition to education and experience, design engineers must possess certain skills and abilities. These include problem-solving, critical thinking, creativity, and attention to detail. Design engineers must be able to think logically and systematically, as well as being able to visualize and communicate their ideas effectively. Once you have gained experience and honed your skills, you may want to consider earning a master’s degree in engineering or a related field. This advanced degree will provide you with additional knowledge and skills, as well as increasing your marketability and earning potential.
To become a design engineer, it is also important to stay up-to-date with the latest technology and trends in the field. This may involve attending conferences and workshops, joining professional organizations, and staying current with industry publications.
Finally, becoming a design engineer requires dedication, hard work, and a passion for engineering and design. With the right education, experience, skills, and attitude, you can succeed in this rewarding and challenging field.
What is a product engineering firm?
A product engineering firm is a professional service organization that specializes in providing product development and engineering services to clients in various industries. These firms offer a range of services, including product design, prototyping, testing, and production support, to help clients bring their products to market. Product engineering firms work with a variety of clients, including manufacturers, startups, and established companies, to help them create innovative and competitive products. The product development process is typically a collaborative effort between the product engineering firm and the client, involving input and feedback from multiple stakeholders, including industrial designers, engineers, marketers, and manufacturers.
A product engineering firm provides a range of technical and engineering services, including mechanical design and engineering, electrical engineering, software development, and quality assurance. By combining expertise in product development and engineering with a deep understanding of industry trends and customer preferences, a product engineering firm can help clients create products that meet the needs of their customers and succeed in the marketplace. Whether working on a new product concept or improving an existing product, a product engineering firm provides valuable support and expertise to help clients bring their ideas to life.
What is a product engineering firm?
A product engineering firm is a professional service organization that specializes in providing product development and engineering services to clients in various industries. These firms offer a range of services, including product design, prototyping, testing, and production support, to help clients bring their products to market. Product engineering firms work with a variety of clients, including manufacturers, startups, and established companies, to help them create innovative and competitive products. The product development process is typically a collaborative effort between the product engineering firm and the client, involving input and feedback from multiple stakeholders, including industrial designers, engineers, marketers, and manufacturers.
A product engineering firm provides a range of technical and engineering services, including mechanical design and engineering, electrical engineering, software development, and quality assurance. By combining expertise in product development and engineering with a deep understanding of industry trends and customer preferences, a product engineering firm can help clients create products that meet the needs of their customers and succeed in the marketplace. Whether working on a new product concept or improving an existing product, a product engineering firm provides valuable support and expertise to help clients bring their ideas to life.